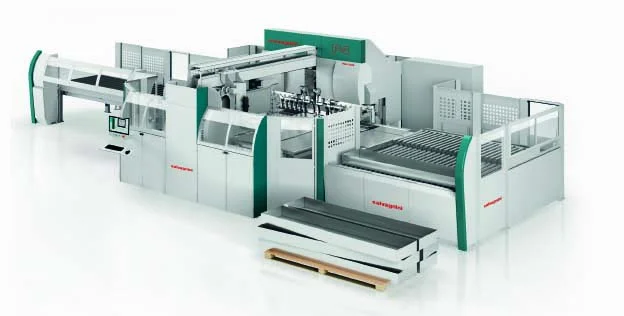
Metal enclosures serve as protective
housings for a wide range of items from
electronics and communication systems
to controls, avionics and critical vehicle
components. Building these boxes to
safeguard their contents from damage
and environmental factors such as dust,
moisture and debris requires specialized
skills that go beyond typical design and
fabrication expertise.
“Very complex enclosures with tough,
highly cosmetic finishes require a unique
combination of engineering experience,
equipment and craftsmanship,” says
Steve Tokarz, president of IMS Engi-
neered Products LLC, a global supplier
of precision sheet metal fabrications and
electromechanical assemblies.
IMS enclosures and AMCO rack sys-
tems can be found in nearly every market
space from transportation, aerospace,
defense and telecommunications to ap-
pliance and agriculture. The Des Plaines,
Illinois-based company carefully put the
pieces in place over time. After acquir-
ing a fabrication business established
in 1974, IMS was founded in 1995. It
then purchased AMCO [started in 1943]
in 2005. Today, IMS stands out as the
preferred choice for businesses seeking
unparalleled quality and reliability.
“We can powder coat, wet coat or
provide a No. 4 finish to complicated en-
closures with very tight tolerances,” says
Tokarz. “We can weld, grind and polish
a component to look like one seamless piece. Our personnel provide a level of
craftsmanship that is phenomenal. From
engineering to fabrication, mechanical
and electrical integration and customer
service, we offer a complete solution.
When it comes to launching new prod-
ucts, we have developed a process with
defined roles and responsibilities. We
know what to do and when to do it.”
MODEL UPGRADE
Equipment such as Salvagnini America’s panel bender technology plays a crucial role in the supplier’s fabrication process. In 2023, IMS installed a Salvagnini P4-3125 panel bender. The capital
equipment investment demonstrated
IMS’s ongoing commitment to lead
the industry in innovation and serve
customers with top-shelf products. The
panel bender’s automatic bending and
handling cycles and universal bending
tools boost throughput for versatile
parts processing. The P4-3125 can bend
panels as long as 10 ft. 2 in. and as wide
as 5 ft. The new panel bender wasn’t the fabricator’s first experience with the OEM.
“We’ve had a Salvagnini panel bender
since 1996,” says Tokarz. “After 28 years,
it was still running until we decommis-
sioned it to install the new one. Our
primary reason for replacing it was that we
wanted to upgrade to newer technology.”
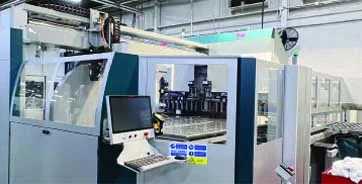
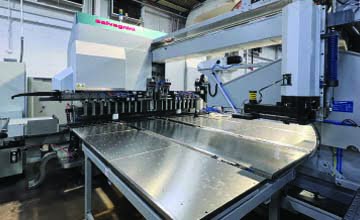
Choosing a panel bender over a press
brake wasn’t a difficult choice. “When you
have the right application, you can run
more parts, faster with a panel bender,” he
continues. “We deal with a lot of large components, doors, side panels. Having the
P4-3125 really helps. Our parts would be too
cumbersome on a press brake. You would
need two operators to hold the material. The
panel bender is more accurate and ergo-
nomic. Upgrading to a newer model was an
easy decision based on our product line.”
Prior to the purchase, Salvagnini ran
test parts for an outdoor power distribu-
tion cabinet that feeds charging stations
for EV vehicles. “Salvagnini proved out
four different parts for us,” says Tokarz. “I
went to Italy to sign off on the machine’s
qualification run. On each end of the side panels there was a 2-in. radius followed
by formed features. The panels are more
than 98 in. long and 4 ft. wide. Salvagnini
had to build a special T tool with specified clearances so that it could form the
radius and clear other features that were
already punched into the part.”
IMS runs stainless, aluminum and
cold-rolled steel on the P4-3125. “We run
all the parts we make for our enclosures
on the panel bender, from the new EV
application to cabinets for medical,
financial, industrial, military, transportation, telecommunications and test and
measurement uses. Appliances are a
huge market space for us,” he says. “What
we like about the P4-3125 is that setup
is quick, and you only have to make a
minor adjustment based off the type of
material being fed into the machine.”
ACCURACY
In addition to controlled centering,
MAC3.0 detects any differences in a
material’s mechanical characteristics
and compares them to its nominal value during the bending cycle adapting the machine and the manipulator’s
movements to compensate for those
variations.
Universal bending tools automatically
adapt in-cycle to panel geometry with-
out downtime or manual re-tooling. This
allows operators to process a range of
machinable materials from 0.02 in. thick
to 0.12 in. thick.
IMS runs mid- to low-volume jobs with
appliance work dictating higher-volume
part runs. Precision and accuracy are cru-
cial, but so is speed.
"The P4-3125 is up to three times faster than a conventional press brake."
Steve Tokarz,
IMS Engineered Products LLC
THE OVERTIME KILLER
“The P4-3125 is up to three times faster than a conventional press brake,” says Tokarz. “The parts we were bending for the EV application took two days and three press brakes versus one day on the Salvagnini panel bender. Labor is also reduced. The press brakes need six guys and two days versus two operators less skilled and one day on the panel bender. My operations manager calls the P4-3125 an ‘overtime killer’ for the forming guys because it just chews through every job put on it. When we compare the P4- 3125 to all the new equipment we’ve purchased recently, we find it’s the best bang for the buck.”
IMS Engineered Products LLC | 847-391-8100 | imsep.com
Salvagnini America Inc.| 513-874-8284 | salvagnini-america.com